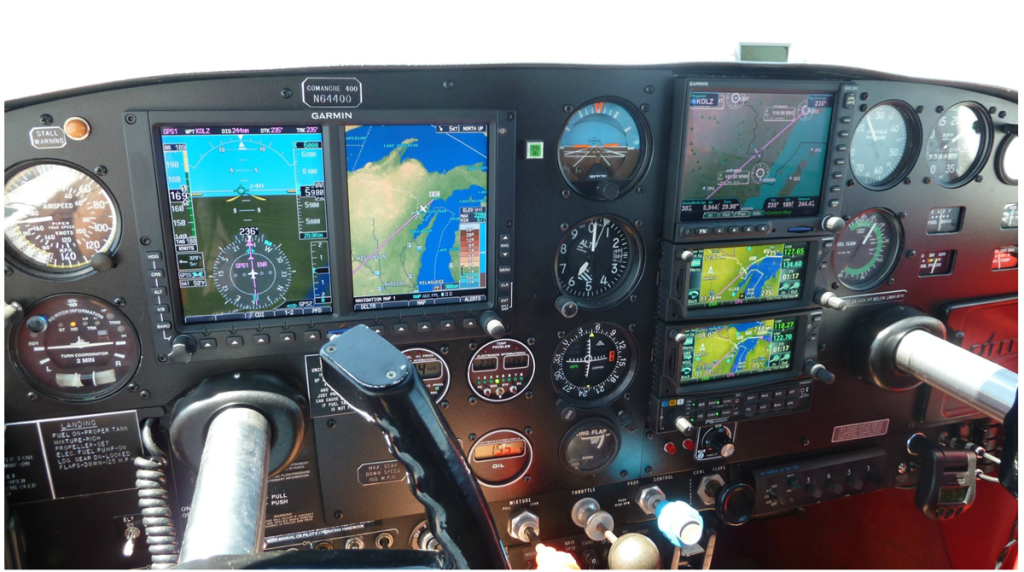
By Bob Hart – www.AvionixHelp.com
There are lots of reasons why an aircraft owner might be considering an avionics upgrade, but it usually is simple: Their current avionics simply don’t meet the mission.
One scenario: You purchased a used aircraft, and the avionics don’t match your plan for it. Of course, it’s always better to find an aircraft that is already equipped for your mission, or as close as possible. After all, if you only get back about 50% of what you invest in an avionics upgrade, then you, as the next owner, essentially paid 50% for it, so this makes dollars and sense, when you can do it.
But we all know what is going on right now in the used-aircraft market. It’s a great time to sell and a tough time to buy, especially if you’re looking for a deal. If you find the right aircraft today, be prepared to pay asking price and move quickly to lock it up. There’s a pilot behind you who is ready to pay more!
Another scenario: You’ve owned an aircraft for years and have abandoned the dream of a faster, roomier plane. You finally decide your plane meets your needs. But you recognize that the old stuff isn’t reliable enough anymore to continue with your present mission, so you either compromise your mission or upgrade the avionics. The good news here is you are likely in better shape financially than the first scenario, and at current aircraft values, you see room to make improvements.
No matter your motive for upgrading your panel, it makes sense to do it right and to know what the aircraft will be worth when it comes time to sell. Remember, you’re putting hours on the engine, which, frankly, has the greatest effect on aircraft values (that and damage history). You also need to know who you are and where you are going.
Pilot, Know Thyself!
There’s VFR, light IFR, true IFR, and business flying. What are you now and where are you heading?
I’m not talking about a waypoint; I’m talking about how you fly now and where you are heading in pilot skills. Also, how deeply you hope to venture into the deep, blue sky — the same sky that turns black in a hurry and is ready to test those skills. Skills alone are not enough. You need to have the tools.
Let’s define what these terms mean, at least for the purpose of this article.
VFR means you fly in nice weather.
Light IFR means you fly VFR most of the time and IFR when necessary. This is always from minimally bad weather (low fog, clouds, or light rain) toward better weather, and a destination with a ceiling at least 500 feet above ground level (AGL). I had about 50 clients in the last 12 months, and 98% are light IFR or working toward that goal. It is my theory that the majority of licensed pilots in the US are light IFR pilots.
The challenge for light IFR pilots is that they can go for long periods of time without any actual IFR flying, and then find themselves needing to do an approach or departure in less-than-ideal conditions. Light IFR pilots could certainly benefit from something like Microsoft Flight Simulator, which will give them the opportunity to “mentally” fly IFR at home, and that can only be good.
True IFR pilots are flying IFR more frequently and have a different set of personal minimums. Pilots who fly for business are likely to take it to the next level with a syndrome similar to “get home-itis” called “get to the appointment-itis.” Each of these pilot classifications requires a different level of skill and equipage, so before you can plan for an avionics upgrade, you have to know where you are, where you are going, what you have, what you don’t have, and what you will need to safely fly your mission. That’s a good place to start.
Equipment Checklist
This article is not about equipment, but a review of the basics makes sense:
A VFR panel only requires a single panel-mounted com/intercom, portable GPS or tablet with software, transponder, and ADS-B Out.
True IFR calls for dual coms, two or three nav sources, sophisticated audio control, autopilot, primary engine management, transponder with ADS-B Out, and ADS-B In (minimum) with a big screen to display it. Also, electronic flight instrument system (EFIS) primary flight display (PFD) or big EFIS flight instruments certainly makes sense here.
Sticking with the premise in the first paragraph, we’ll focus on light IFR, since I think most of you are there or heading in that direction.
Light IFR also requires, in order of priority:
The rest of this article can be seen only by paid members who are logged in.Have a website login already? Log in and start reading now.
Never created a website login before? Find your Customer Number (it’s on your mailing label) and register here.
JOIN HERE
Still have questions? Contact us here.