If you follow my articles, you know that I am one of the few avionics writers who talks about street price (equipment) and estimated installed pricing (equipment plus labor). Frankly, I think that’s exactly what you want to know when you’re shopping for an avionics upgrade. A part of my “service” to my consulting customers is showing them how best to shop for an installation and taking a critical look at the install quotes they get after my report. Clint Eastwood would be pleased. The “good, the bad, and the ugly” are alive and well in the avionics quotation business! To do this with reasonable accuracy, you need to know the install labor rate and the estimated number of hours that a task should take. To keep a handle on hourly labor rates, I consult the Aircraft Electronics Association, or AEA as it is better known. The AEA, with more than 1,300 member shops, is a support organization for avionics shops across the country and beyond. AEA members share their used avionics inventories, get help on regulatory issues, and, in this case, find out what the industry and their competitors are charging for avionics repair and installation. They get this information through the AEA’s annual Rate and Labor Survey of its members. The 2019 survey shows rates from across the country and, yes, if you want to know how much your avionics technician is likely getting paid, it’s in there also but only available to members. I think most of us really are only interested in how much we pay and not how much they make.
What causes rate variance?
Surprisingly, install rates do not differ much from shop to shop but regions (east versus west) do a bit. Of course, when we switch from GA to corporate, we see a big jump!
In the quotes I see, I see shops trying to hide their labor rates by quoting you the total labor cost without telling you the number of hours. Without the rate, it is easy to fudge a little on labor estimates. Fact is, while labor rates don’t vary much, labor hours can vary greatly from shop to shop. From my years of quoting installs (the shop dictates the hours, I just quoted them), I began to understand how much time a task takes. I combine my past knowledge with the current quotes I see from my clients. When I see labor hours that seem to be out of line, I will usually consult with a shop I trust. Just before EAA AirVenture Oshkosh 2019, a client sent me a quote that, in my opinion, had an extra 75 labor hours; that’s an extra $7,500! I took the quote with me and consulted with Tony Polemarkis of Avionics Place in Rockford, Illinois. Avionics Place is one of those shops I trust. Sure enough, Tony saw an extra 60 hours of labor in the quote. I suggested that my client get more quotes: That’s about the only defense against a high quote. In some cases, that shop is still the right shop for you because of location. So, you take a fair quote back to them and renegotiate.
In many cases, I’m right on but I also learn as I go sometimes. Here’s an example. S-TEC has been the dominant aftermarket autopilot manufacturer for years. They previously published the estimated hours it should take to install their legacy, analog autopilots. I have been using that data until recently when I discovered that S-TEC/Genesys and Garmin no longer provide a finished wiring harness with their 3100 or GFC autopilots. Their previous models did and still do include a completed harness. With the GFC and 3100, installers must create them and that can add an extra 10 hours from previous estimates. So, let’s talk install rates, estimated labor hours for a given task, and how best to shop for an avionics installation.
Hourly labor rates
“Go west young man” does not apply here. The farther west you go, the higher install labor rates for avionics go, but not by a significant amount. As you might expect, with the “rush” on ADS-B and the associated panel upgrades, rates went up compared to the previous year. Here’s what install rates looked like in 2019 according to a survey of AEA members (thank you to the Aircraft Electronics Association for this data).
Service is likely repair of an existing installation and not necessarily a bench repair.
Install is obvious.
Engineering would be that portion of an installation that requires drawings and/or wiring diagrams often required by the FAA on field certifications.
Instrument would refer to instrument shops that operate on different licensing.
For the most part, the labor rates that I am seeing in 2020 shadow the 2019 rates. The COVID-19 virus probably interfered with most shops plans to increase their rates in 2020.
Estimated installation hours
As I mentioned at the top, this knowledge base comes to me from quoting installs during my days at Eastern Avionics and APG Avionics and from reviewing recent install quotes I get from my clients. I’m frequently asked by pilots, especially those who would like to do upgrades in phases, if doing it all at the same time will save money versus doing some now and some later. The answer in most cases is no. Upgrading an IFR GPS for example, a popular upgrade, is a task in itself, as is the installation of an audio panel, transponder, or nav/comm. There can be some savings doing more now when the interior must be removed and replaced. That is a day’s work in itself so avoiding messing with the interior more than once will not only save you a little money but also saves wear and tear on the interior itself. Some pilots recognize this and opt, with the shop’s approval, to remove and reinstall the interior themselves.
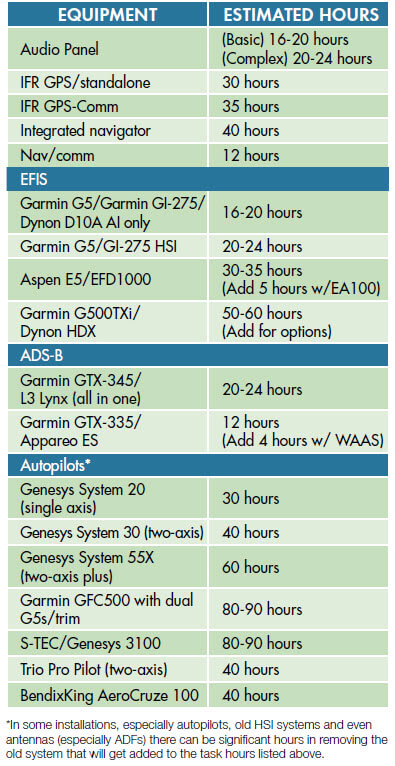
Panel re-creation
Let’s face it, in the ’60s, Piper really had no grasp on what to expect we would see in a GA aircraft panel. Key gyro instrument locations were off and avionics were tucked away in locations that also made no sense. By the ’70s, manufacturers did much better but still — those plastic overlays! I think it was the ’90s before we saw the end of plastic and the all-metal panel come along. Unless you are trying to maintain that “legacy” look, metal is desirable but at a price. I see different approaches. Some owners go for a new pilot panel and a separate co-pilot panel, but the best look and the most available “landscape” comes with a one-piece panel, powder coated, and silk screened. If big EFIS is in your plan, a new panel is mandatory but pilots who are investing significantly and often with a long-term plan for the aircraft will chose to upgrade the panel at the same time. You should be able to do this in a Piper single in the $2,500 range, but larger or more complex aircraft can get pricey. A recent client with a Piper PA-46-350 Malibu JetPROP (turbine conversion) got a quote of more than $10,000 to redo his panel. We re-shopped and the final quote from another shop was about $5,000. There’s a lot of stuff in a turbine JetPROP panel loaded for IFR “Bear”!
Shopping for an installation
Let me start with an analogy. “Hi, I need to get my house painted and I heard you do good work. I’m located in another state and I wonder if you can give me a quote over the phone. I can send you pictures and colors I’m considering.” Sounds crazy but, in reality, this is a way too common method that aircraft owners use to get an avionics quote. If you were the painter (and crazy enough to even quote this) you would add a significant financial margin to the quote for “unknowns.” An avionics shop, quoting long-distance without seeing he aircraft, will likely do the same. When the job is done, and no “unknowns” have surfaced, don’t expect the shop to credit you for “no unknowns.” There is no place on the invoice for that. So, if you want the best price, make an appointment and fly in to give the shop a chance to look over your project. If you’re flying a legacy single and the shop’s tarmac is loaded with corporate queens, you are probably in the wrong place. Ask around, check the forums, and find a shop that “relates” to your aircraft. The priorities are to get a fair price and good quality work. If you’re on a legacy budget and you hope to also get it done fast, you are pushing too hard. Good, fair, and fast — in life and in avionics, you usually only get to pick two. While you are getting a quote, use the opportunity to “size up” the situation. Is this a person you can work with? Would you want your airplane here?
You are the customer, although when shopping for avionics work it doesn’t always feel that way. Here are a few things you want to specify in your written quote. First, what is the shop’s hourly rate for installation. As I mentioned before, some shops seem to try and hide that — ask. Also, you want the shop to break down the equipment cost and the labor costs separately.
If you get more than one quote (and in most cases you should), it will be easier to compare if equipment and labor are separated. You also want to get a good idea of when the shop can start the work (once you make a decision) and approximately how long the project will take. Be patient on the latter! There’s an old saying among avionics installers: “Never enough time to get it done, always enough time to do it over!” This is even more important if you are traveling some distance to get this done. Trips back and forth to fix things will get expensive fast (and wipe out any savings), which is another reason finding the right shop closer to home almost always makes the most sense, even if they are not the lowest price.
Most shops will ask for a deposit up front just to put you on the schedule and they will want more money, usually enough to cover the equipment cost, when you drop off the airplane. You’ll pay the balance of the labor when the project is complete. This is also a good time to discuss warranty. New equipment comes with factory warranties, but you’ll want to know how long the shop will stand behind its work.
While the equipment is being installed is a good time for you to be getting your head into the pilot’s guides and user manuals for your new equipment. It’s not the shop’s responsibility to teach you how to use the equipment — although some shops are better at this than others. If you are making a significant investment, which includes a new autopilot, a test flight is in order and will also serve to introduce you to the basic features so pay attention!
Conclusion
It is likely that the biggest variable you will see between avionics installation quotes is the labor hours. Labor rates within a region will generally be close but the number of hours that a shop will assign to a task can very greatly. We did not mention sales tax, but that is a factor in some cases. A recent client in the Atlanta area decided to shop for his install in Florida because Florida, like many states, has an exemption on sales tax for aviation repairs and installations. That can really add up on a significant upgrade! The bottom line is, do your homework or get professional help (like Avionix-Help.com) and shop smart. Over the phone or by email is not the way to get a “fair” quotation. Do the work. Push for a fair price and quality work and be patient on time.
Until next time … safe and happy flying!