On Oct. 19, the FAA released a SAIB (Special Airworthiness Information Bulletin) regarding wing spar cracks in Piper PA-28 and PA-32 aircraft. The bulletin isn’t a required AD (Airworthiness Directive) but, rather, updates plane owners, operators, mechanics, and inspectors about information gathered from inspections required by AD 2020-26-16, which was issued in 2020 because of a fatal accident in 2018 caused by fatigue cracks that led to a wing spar failure. That AD required a one-time, eddy current inspection of certain lower spar cap bolt holes.
Results of the inspection required by AD 2020-26-16 indicate that the problem is widespread enough to likely warrant another airworthiness directive and that one goal of this SAIB is to gather more information. A future AD may require frequent inspection of aircraft that have already been inspected and may require additional planes to be inspected.
The FAA recommends that owners and operators provide additional information and feedback on the availability of qualified eddy current inspectors, how Factored Service Hours (FSH) are calculated, reporting cracks or damage not already reported, and other feedback on information covered in the SAIB. The full SAIB includes the contact details for submitting information and feedback.
Participate in this discussion on our forum here.
What’s below is an online-article version of this service letter, which was issued by the FAA via a PDF. Read or download a PDF of what’s below by clicking here.
The FAA Bulletin starts below.
SUBJ: Wing Spar
SAIB: 2022-20
Date: October 19, 2022
This is information only. Recommendations aren’t mandatory.
Introduction
This Special Airworthiness Information Bulletin (SAIB) alerts all owners, operators, maintenance technicians, and inspectors of Piper Aircraft, Inc. (Piper) PA-28 and PA-32 airplanes of information gathered as result of a fatal accident of a Piper Model PA-28R-201 airplane in 2018 and the inspection findings that followed. The accident, determined to be caused by fatigue cracks in the lower spar cap, resulted in the Federal Aviation Administration (FAA) issuing Airworthiness Directive (AD) 2020-26-16, which requires several actions including a one-time inspection of certain lower spar cap bolt holes. AD 2020-26-16 was issued as an interim action and requires reporting certain inspection information to the FAA to help determine the number of cracks present in the fleet. The inspection reports received by the FAA thus far indicate the presence of numerous cracks and hole-quality issues in a significant number of airplanes.
The FAA is concerned that the presence of cracks and other hole-quality issues could lead to additional in-flight wing separations if additional actions or modifications are not taken. Analysis of the AD inspection data along with additional analysis by various contributors, including Piper and the U.S. Air Force, is guiding the FAA to develop further corrective action. These analyses are indicating a possible need for frequent inspections, and inspections of additional airplanes beyond those initially inspected per AD 2020-26-16, to ensure proactive detection of fatigue cracks.
The FAA has determined that this airworthiness concern is an unsafe condition that warrants AD action under Title 14 of the Code of Federal Regulations (14 CFR) part 39. The actions specified by this SAIB are not mandatory, however, the information requested by this SAIB will help the FAA develop an AD action to address this unsafe condition.
Background
As stated above, the FAA issued AD 2020-26-16 due to a 2018 in-flight wing separation on a Piper Model PA-28R-201 airplane caused by fatigue cracks located in a visually inaccessible area of the lower main wing spar cap. Inspection of another airplane in the same fleet of the accident airplane (manufactured at a similar time and operated in a similar training mission) was also found to have cracking in the wing spar. The National Transportation Safety Board (NTSB) found fatigue cracking across an extensive cross-section of the lower spar cap. The crack and failure occurred across the T-section at the two most outboard bolt holes attaching the lower spar to the wing box (see Figure 1).
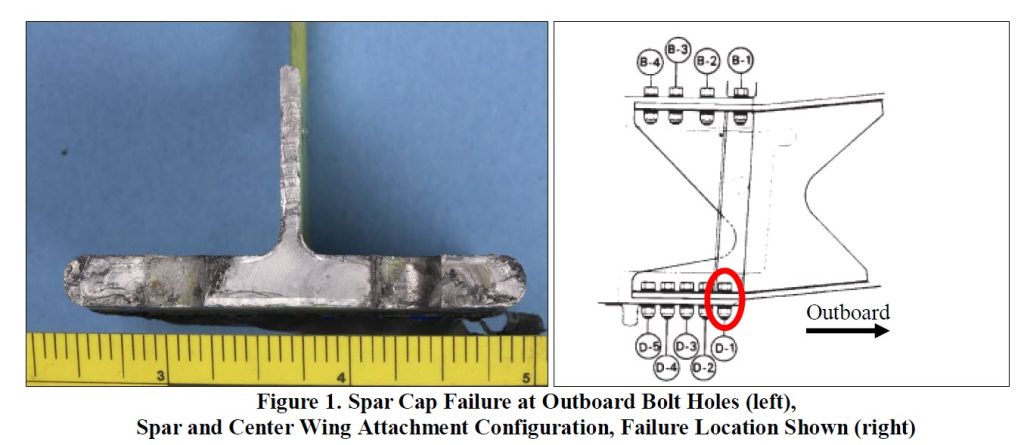
AD 2020-26-16 requires a one-time eddy current inspection of certain bolt holes of spars that have reached 5,000 factored service hours (FSH), and a reporting of the inspection results to the FAA and Piper. The inspections were required for the most outboard set of bolt holes, both forward and aft (see Figure 2). The eddy current inspection method is a non-destructive technique that utilizes electromagnetism to detect flaws on and under the surface of a part in question. The inspection method has certain limitations including the depth in the material where a flaw can be detected, the size of the flaw, and that a highly skilled and properly trained inspector is required, but it is a proven tool that is commonly used for inspections of this nature. The eddy current inspection method is capable of detecting cracks, but is also sensitive to surface anomalies that may cause cracks to form in the future, such as corrosion or gouges. Visual inspections are not sufficient to detect such cracks.
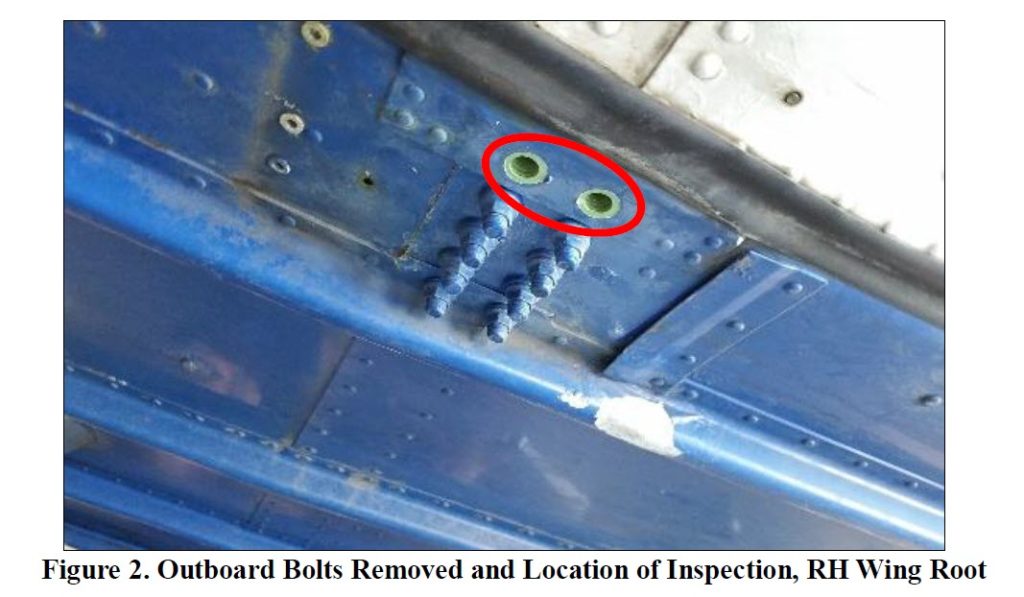
The FAA and Piper received reports on approximately 2,880 airplanes. Out of these, 115 airplanes were reported as having crack indications. Approximately 25 percent of these indications were later confirmed to be hole damage or corrosion and not a crack. The remaining indications include a mix of unconfirmed indications, but fatigue cracks were also identified, including some examples shown in this SAIB. Unconfirmed crack indications were found in airplanes with as little as 3,264 hours time in service (TIS) on a Piper Model PA-28R-180 airplane, but has not yet been confirmed. Figure 3 shows a summary of the positive indication inspection results received by the FAA and airplane models involved in accidents attributed to or potentially related to the spar cracking issue. In addition, some owners and operators of airplanes not included in the AD’s applicability voluntarily inspected and reported findings of crack indications in the wings of their airplanes (not shown).
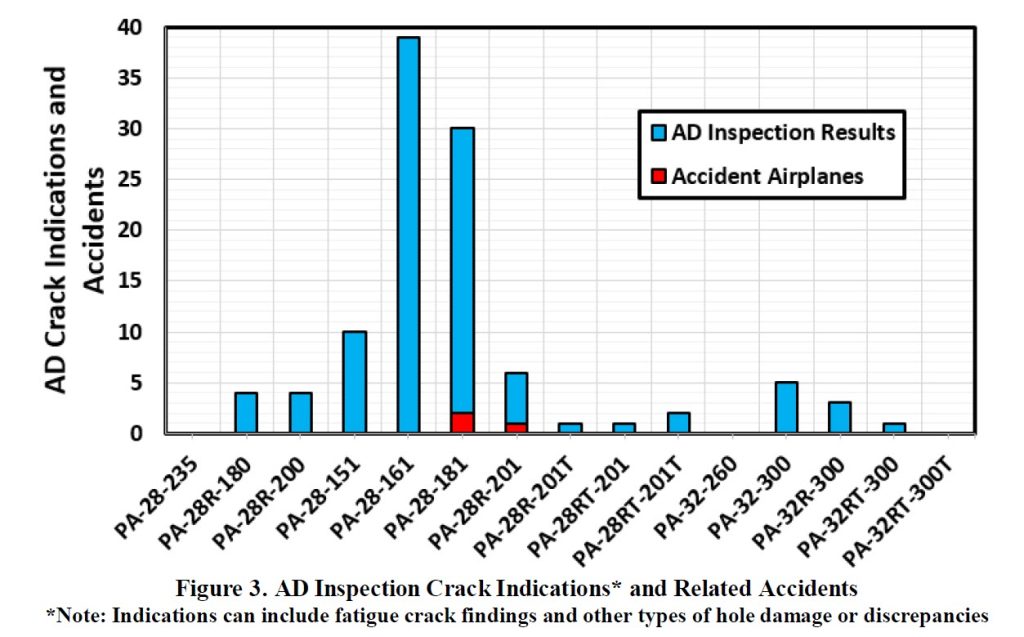
While there are a large number of crack indications in the inspection results, it is possible the inspection can result in a crack indication due to something other than a confirmed crack, such as mechanical bolt-hole damage, corrosion, or some other type of discrepancy. Some examples of the types of spar damage findings are shown in Figures 4 through 9. AD 2020-26-16 eddy current inspections successfully identified bolt-hole mechanical damage allowing for corrective action to be taken before that damage could lead to cracking, which could lead to a wing separation. Multiple NTSB laboratory examinations have shown that cracks have formed due to internal hole anomalies as well anomalies adjacent to the hole. The 2018 accident showed multiple crack origins at the hole inside diameter.
A challenge of the eddy current inspection is that corrosion or damage may indicate a crack when no crack exists. However, it is important to note that a concerning number of confirmed cracks have been found that were fatigue related and not related to mechanical damage. The FAA has not confirmed all of the crack findings, but believes there would still be a mix of confirmed cracks and other bolt-hole discrepancies. The FAA believes that the sensitivity of the eddy current inspection is necessary in detecting cracks because of the small critical crack size in this spar as calculated by the U.S. Air Force and documented in NTSB reports.
Participate in this discussion on our forum here.
The AD 2020-26-16 inspection reports indicate that additional corrective action beyond that required by AD 2020-26-16 is likely needed. While AD 2020-26-16 addresses the immediate safety concern, due to aging, more airplanes will need to be inspected, and the airplanes already inspected will need additional inspections. Additionally, the FAA may consider establishing a life limit on the wing spar for the high-time severe usage airplanes. This life limit may be similar to the life limit imposed on Piper PA-44 airplanes. The Piper PA-44 airplanes, which have a similar wing spar attachment design to the Piper PA-28 and PA-32 airplanes, have a life limit on the spar based on normal usage of 14,663 or 16,462 hours TIS, depending on the model.
Aircraft aging, due either to hours TIS or usage, is an issue that needs to be addressed for every fleet at some point. Small imperfections can exist in aircraft structure from an early age; however, through operation, these imperfections can slowly grow into fatigue cracks. Crack development is a function of many factors, including design of the structure, how severely the aircraft is flown, and manufacturing processes. Fatigue cracks have the effect of weakening the structure and its ability to support the stresses the aircraft is originally designed to handle.
The 2018 accident, and the AD 2020-26-16 inspection reports indicate an aging fleet that requires intervention to ensure the damage does not reach a critical state prior to being detected. At a minimum, this typically takes the form of repetitive inspections to be able to capture the formation of a detectable crack, requiring repair or replacement.
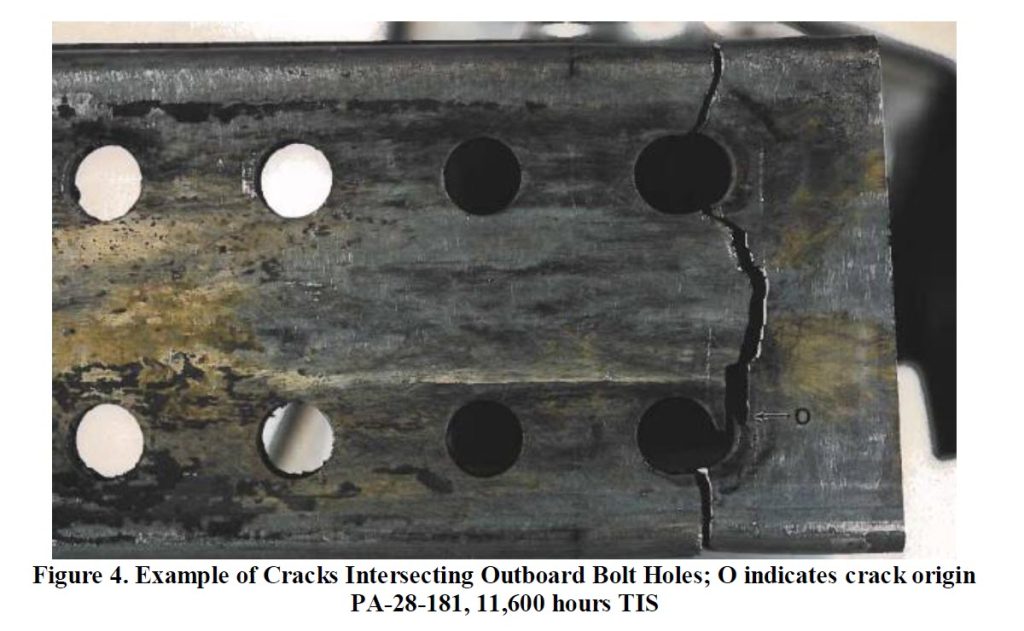
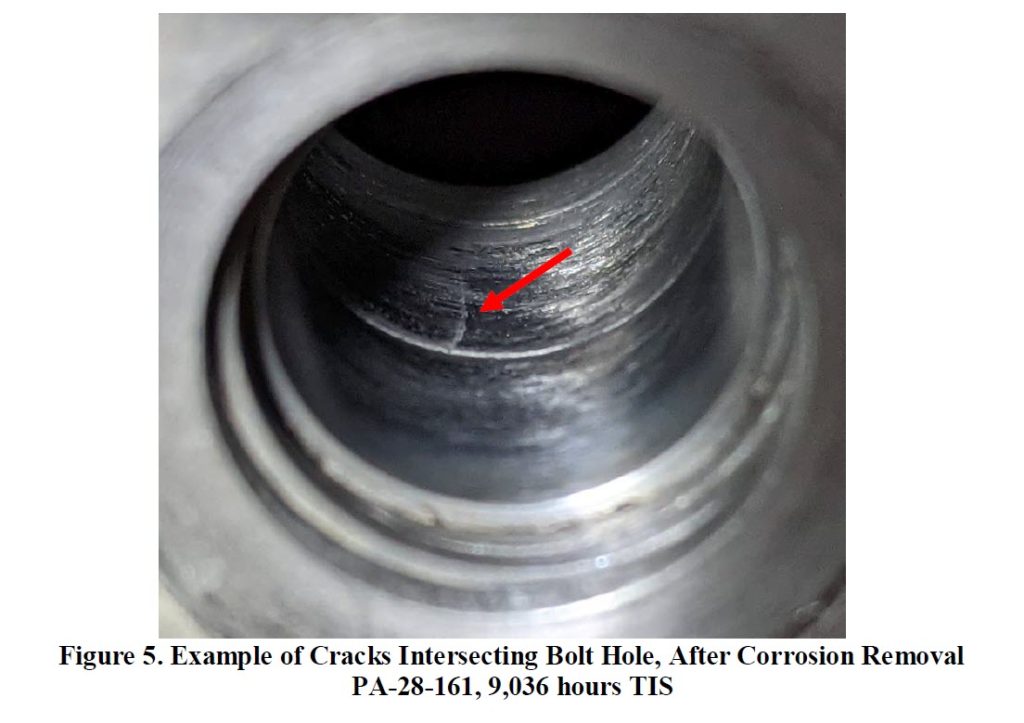
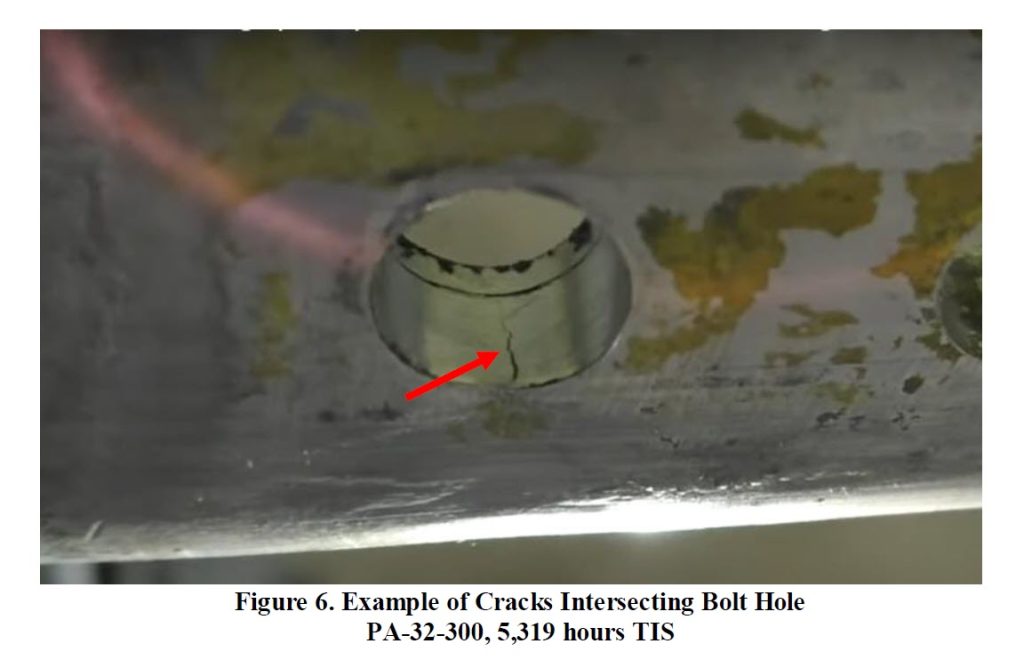
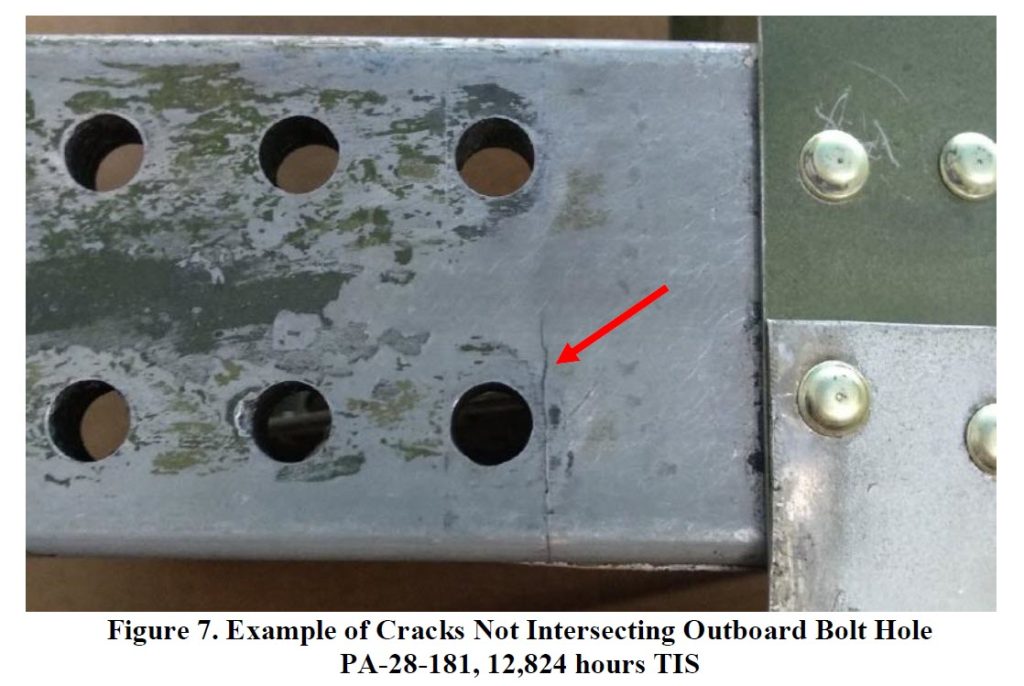
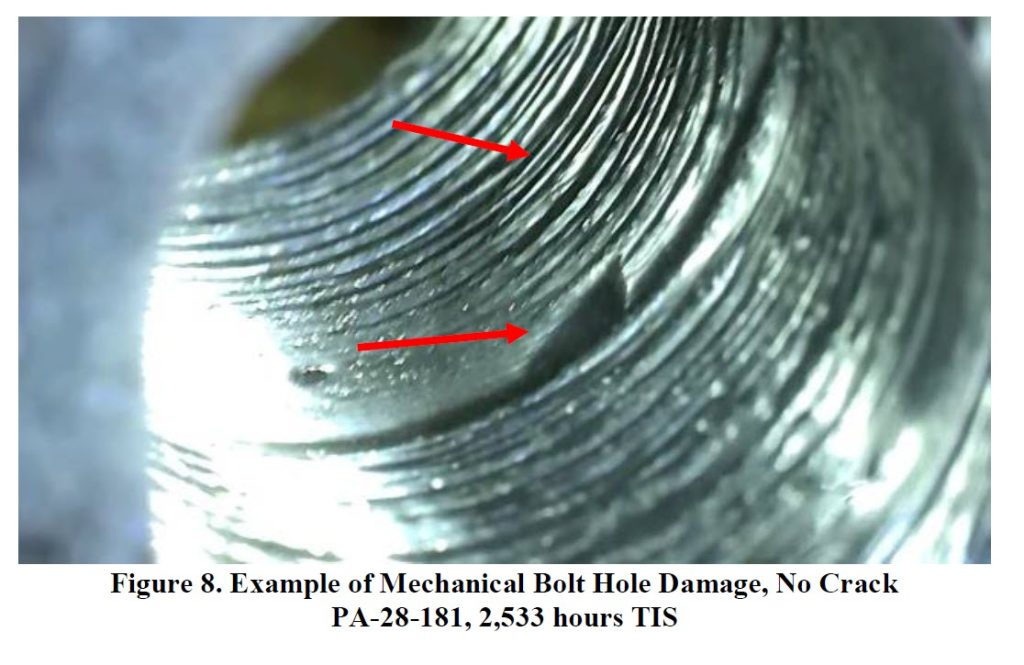
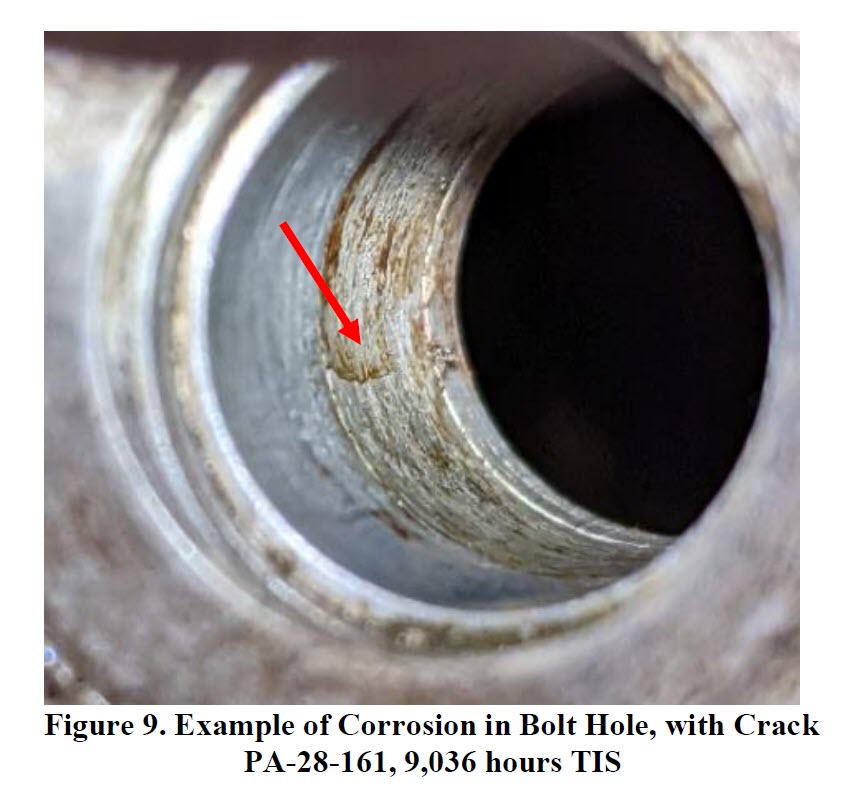
Accident and Corrective Action History
Including the most recent accident in 2018, three accidents have occurred where fatigue cracking in the lower wing spar was the cause or was found during the accident investigation. These accidents and the inspection results from AD 2020-26-16 provide valuable knowledge that can be applied to determine appropriate corrective actions. As a result of the 2018 accident, the FAA is studying the inspection results of AD 2020-26-16 and other field data to determine if additional spar inspection criteria are needed to address the aging fleet.
Accident No. 1, described in the next paragraph, resulted in the FAA issuing AD 87-08-08. This AD required several actions including removing and dye penetrant inspecting the wing for cracks. Similar to AD 2020-26-16, AD 87-08-08 resulted in many inspections; however, unlike recently, only a few cracks were found, likely due to the low hours TIS of the fleet at this time. At the time, the FAA determined the cracks found as a result of the inspections required by AD 87-08-08 only developed due to the airplane’s severe flying usage or previous repairs, and as a result the AD was rescinded in May 1989. While this AD rescission may have been appropriate at that time given that this was a low hours TIS fleet, these assumptions cannot be applied equally now. Given the current age of the fleet, both aircraft usage and hours TIS must be considered, and aircraft must be inspected for fatigue cracking.
Accident No. 1: 1987 – Marlin, TX – NTSB Accident #: FTW87FA088
The first related accident occurred in 1987 in Marlin, TX. The accident airplane was a Piper Model PA-28-181 airplane with 7,490 hours TIS. Nearly all of this airplane’s flight time was known to be spent in a “Pipeline Patrol” mission. This type of mission is characterized by very low altitude and terrain following flight profiles. These flying characteristics degrade an aircraft’s structure faster than most other missions. See Figure 10 for a view of the accident airplane’s failed spar, where “O” indicates fatigue crack origins and “W” indicates a web fatigue crack.
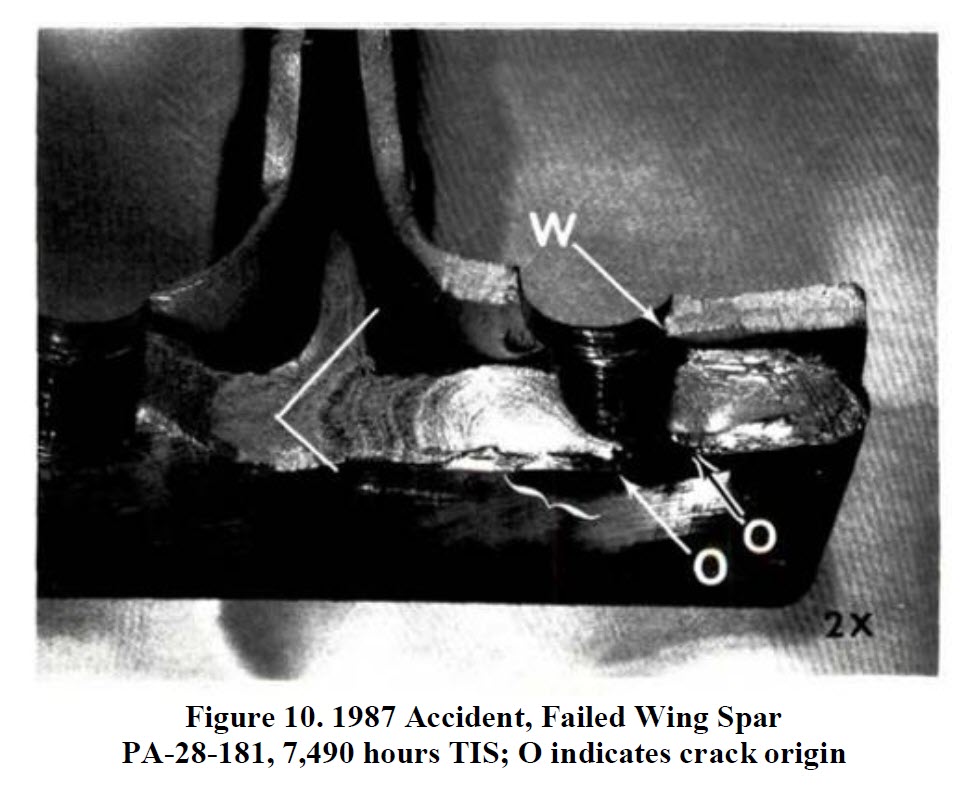
Accident No. 2: 1993 – Provincetown, MA – NTSB Accident #: NYC93FA140
The second of these accidents occurred in 1993 in Provincetown, MA. The accident airplane was a Piper Model PA-28-181 airplane with 11,683 hours TIS. This accident was attributed to weather with signs of structural overloading, but a fatigue crack was also found in the failed spar. The crack is beyond the critical crack size later calculated for that spar. While the NTSB did not identify the fatigue crack as the probable cause of the accident, its presence may have contributed to the effect of the structural overload. At the time of the accident, the airplane was being flown for personal use; however, the airplane was operated by a company providing a mix of training and charter flights. The training mission type of flying is characterized by low altitudes and many takeoff and landing cycles. While less severe than a “Pipeline Patrol” mission, the training mission would contribute more towards fatigue than personal use. See Figure 11 for a view of the accident airplane’s failed spar near a bolt hole, where “O” indicates fatigue crack origins. The origin in this case was adjacent to the hole, not in the hole, as in the 2018 accident.
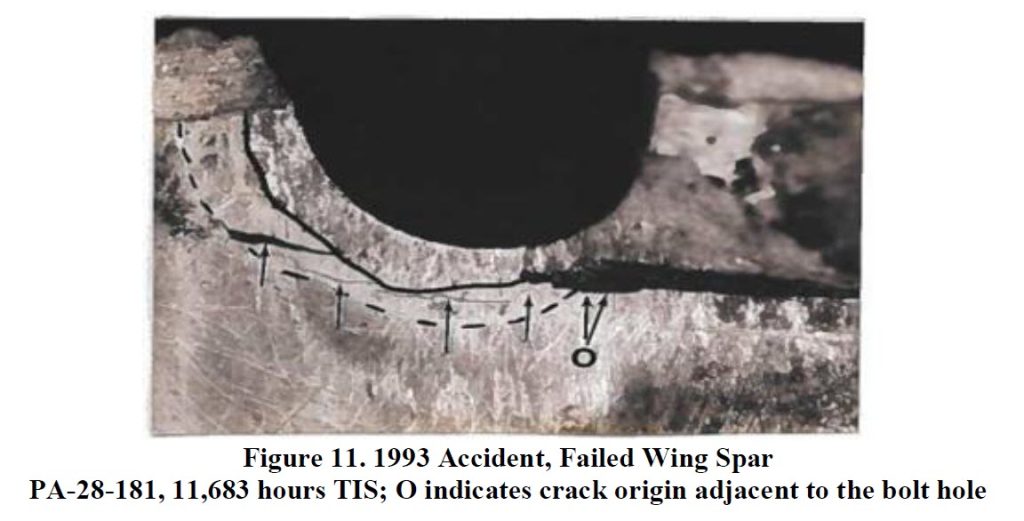
Accident No. 3: 2018 – Daytona Beach, FL – NTSB Accident #: ERA18FA120
The third and most recent of these accidents occurred in 2018 in Daytona Beach, FL. The accident airplane was a Piper Model PA-28R-201 airplane with 7,691 hours TIS. This airplane was used almost exclusively for flight training throughout its lifetime. This type of usage is expected to reduce the fatigue life of the airplane more than an airplane used as a mixture of personal and training, while still less damaging than use exclusively in the “Pipeline Patrol” mission. See Figure 12 for a view of the accident airplane’s failed spar.
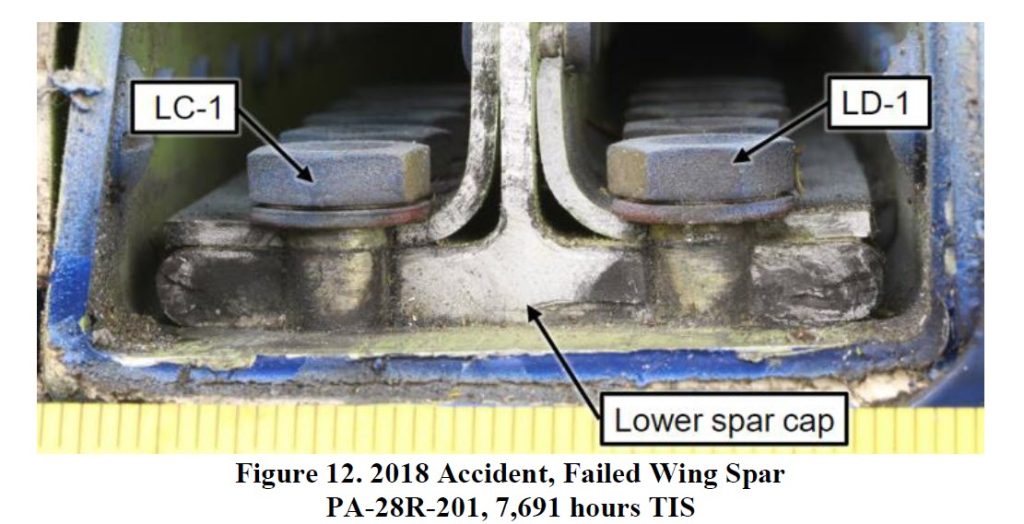
Recommendations
The FAA is recommending that owners and operators provide the following information. Reporting is voluntary. The FAA will analyze the information received to determine further action. As part of its commitment to continued operational safety, the FAA is monitoring the Piper PA-28 and PA-32 airplanes for issues related to lower main wing spar cap cracks and requests submission of such reports to the person listed under For Further Information Contact (bottom)
1) Availability of Eddy Current Inspectors
The FAA is concerned about the availability of eddy current inspectors to perform inspections of the high-time airplanes. The FAA recommends providing information regarding the number of inspectors, including Level 2 and Level 3, available to perform inspections similar to those required by AD 2020-26-16.
2) Factored Service Hours (FSH) Feedback
The FAA has received both positive and negative comments about the FSH approach to setting the inspection threshold for AD 2020-26-16. By using a factor, the intent was to target inspections to the airplanes that were most likely to be engaged in training, which was one of the risk factors identified. While this necessitated some complexity in the calculation of inspection times, it significantly reduced the cost of inspection for personal use airplanes. EASA AD 2021-0107R2 uses a different method for determining factored service hours because in the European Union all aircraft are required to complete 100-hour inspections regardless of the operational requirements. In the United States 100-hour inspections are only required when operating for hire. In the FSH calculation, the EASA method accounts for age of the airplane whereas the FAA AD 2020-26-16 method accounts for a combination of age and the number of 100-hour inspections. The EASA method was developed to account for the FAA’s FSH method under the European Union regulatory system. We appreciate any feedback on the practice of using an FSH, and what the factors should be in the equations embedded in any future inspection thresholds and intervals. The EASA AD is available at ad.easa.europa.eu.
3) Cracks or Damage Not Already Reported
The FAA recommends reporting any crack(s) or damage found in the wing spar bolt holes if not already reported to the FAA or Piper per AD 2020-26-16 or other means. Please provide the airplane model, serial number, hours TIS, number of 100-hour inspections, photographs and a description of the damage found in any wing spar bolt hole.
4) Other Feedback
The FAA welcomes any additional feedback on what has been discussed in this SAIB.
For Further Information Contact
Fred Caplan, Aviation Safety Engineer, Atlanta ACO Branch, FAA, 1701 Columbia Avenue, Atlanta, GA 30337; phone: (404) 474-5507; email: frederick.n.caplan@faa.gov.