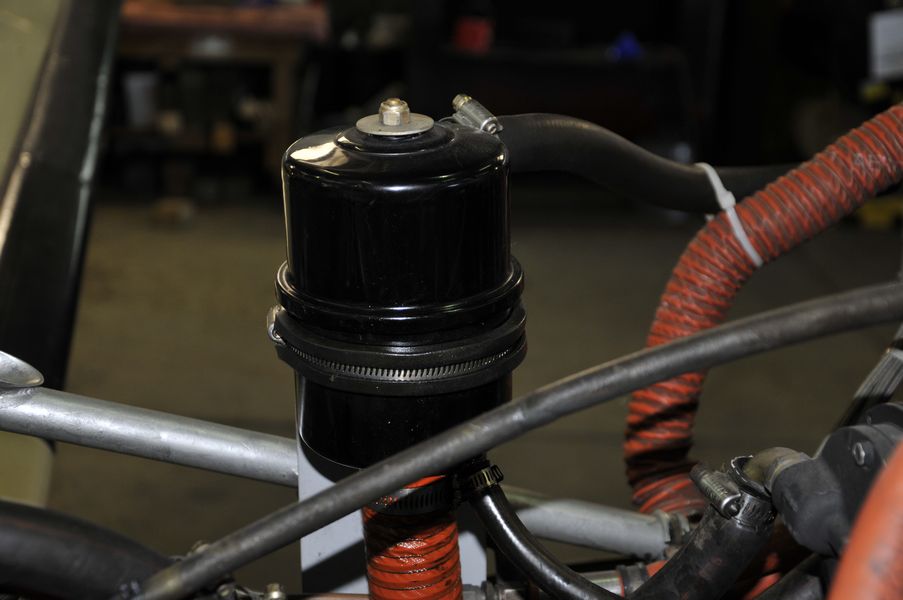
Why you should not install an air-oil separator: Read the first article below.
Why you should install an air-oil separator: Scroll to second article below.
Enter the conversation: Join the discussion in the forum.
Why You Probably Don’t Need an Air-Oil Separator
By Erich Rempert
Piper Owner Society A&P/IA
Sometimes you’ll be kicking tires — either on the Internet or on a ramp somewhere — and you’ll see or hear that an airplane has an “air-oil separator” listed as one of its specs. If you’re unfamiliar with the part, you think: “What is that and what does it do?” You may even question why your plane doesn’t have one and begin wondering if you should have one installed.
An air-oil separator is meant to do just what the name suggests — separate the oil and air; ideally, returning the oil to the engine sump and the air to the atmosphere. They were devised and employed back in the heyday of wet-vacuum pumps. A “wet” pump is one that is not segregated from the accessory case via a seal (Garlock seal) and it allows engine oil into the vacuum pump vanes for lubrication. This provided longer life and a better seal on the high-volume vacuum pumps that were necessary for vacuum-powered autopilots like the Brittain.
These autopilots needed a ton of air because their servos were actually vacuum bellows that pulled cables and moved the controls. Due to the volume of air needed to make up for inherent leaks, vacuum-powered gyros and the servos, the pumps had to work very hard and thus needed internal lubrication. They literally sucked in oil, moved the oil though the pump, and blew it out the pump exhaust, along with the air that was used to run the gyros and servos. This amounted to a “total loss” lubrication system, as all the oil used to lubricate the pump was blown overboard. This spawned the need for a way to recover the oil used for lubrication and put it back into the engine, and so was born the air-oil separator (AOS).
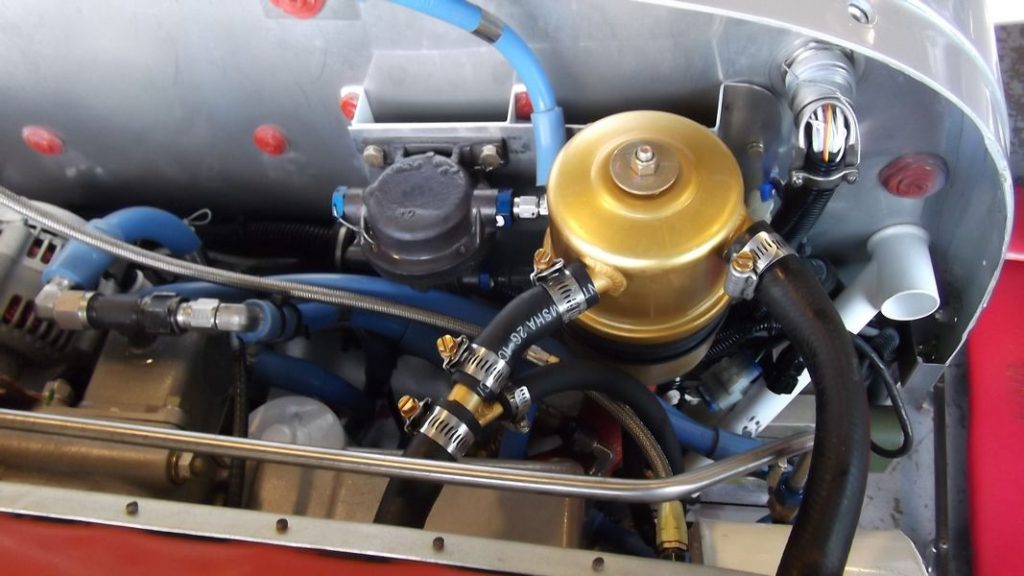
How an Air-Oil Separator Works
An AOS works by directing the exhaust blown from the vacuum pump into a big can filled with a medium similar in composition to that of an S.O.S scouring pad. Inside the can is a large stand pipe (usually in the center) with a section of SCAT tubing attached. On the outer parimeter of the can (in the lowest spot) is a hose that leads back to the crank case. The tubing acts as the exhaust for the air, while the hose allows the recovered oil to return to the sump.
The exhaust from the vacuum pump blows into the can with tons of oil droplets in suspension. The oil smashes into the S.O.S. pad and becomes stuck to it, as the air moves through the pad and out the large exit atop the stand pipe, while the oil suffers from gravity and drains back into the engine. Genius!
Experimentation showed however, that often crank-case pressure prevented the oil from the separator from flowing back into the sump. It was also found that in some instances a great deal of oil was being lost out the crank-case breather tube as well. Later systems routed the breather tube through the canister thus allowing recapture of the oil lost out the breather due to blow-by, and negating the pressure differential issues preventing free flow of return oil, while still venting the excess pressure and water vapor held in suspension overboard.”
And to further alleviate the issue of crankcase pressure preventing free flow of oil back into the sump, often a tube off the pressure side of the vacuum pump was plumbed into the oil return to create a Venturi-like suction to draw oil back into the engine.
Simple theory, simple design, lots of hoses … but pretty straightforward and maintenance-free. Modern “Instructions for Continued Airworthiness” (ICA) will require you to disassemble and clean the AOS every 100 hours or 12 months to prevent blockage, etc., but that’s very minimal.
So why doesn’t my plane have one?
Well, if you don’t have a wet vacuum pump you shouldn’t need one. Dry vacuum pumps (the vast majority of those in service today) have graphite vanes and do not require any lubrication at all. In fact, moisture in the pump usually leads to catastrophic failure, i.e. the vanes shattering and destroying the pump.
So why do you still hear about airplanes that have AOS? Well, the theory is that they recover any oil blown out the breather tube and thus the engine only loses the oil it burns, meaning they are used as a means to reduce oil consumption.
So, I ask, does your engine use a lot of oil? If it does, why does it use oil, and how is it losing oil? If the oil is lost through combustion, an AOS will do absolutely nothing to solve that problem. If your engine is blowing excess oil out the breather, an AOS may prevent you from losing that oil, but really at best it’s a band-aid for some other issue.
My IO-470 Continental-powered Navion will throw all oil out of the sump down to about nine quarts. At around nine quarts (out of a possible 12) it stabilizes and will stay there for 40-plus hours.
If I add a quart when it gets to nine, within an hour or two it will be gone. However, it takes a long time for it to dip below nine. So, the question is: If you have an engine that is throwing oil out the breather as fast as you can add it, is the answer to buy an STC’d kit, pay a mechanic $100/hour to install it, do a major alteration, and then file the paperwork?
Or is the answer to find out the oil level at which your engine is happy, or figure out if in fact the engine is not happy at all?
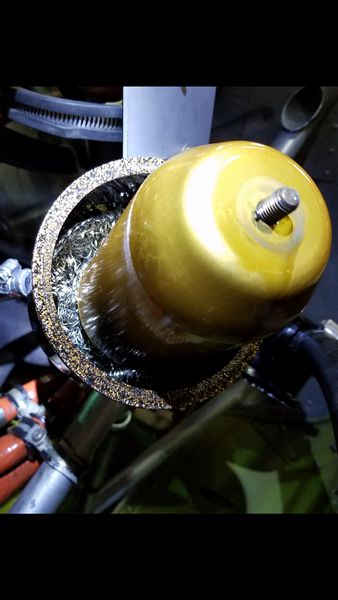
What To Do When Oil Disappears
Most engines are perfectly safe to fly with two-thirds to three-quarters of their total oil capacity, but what if you get to two-thirds and the level keeps getting lower … uncomfortably low?
Well the answer is you need to find the cause. Excessive crank case pressure can be caused by a number of things, but they mainly fall into four categories:
Enter the conversation: Join the discussion in the forum.
- Aerodynamic forces in flight are pressurizing the crank case. An example would be a timing plug left out of the engine case or an oil cap left off on the high-pressure side (inlet) of your cooling system.
- Aerodynamic forces in flight are sucking on the crank case. An example would be a breather tube that is protruding into the slip stream with no vent slot cut into it in the engine compartment, creating a vacuum insidethe engine.
- Excessive combustion blow-by. Examples include worn rings, broken rings, and worn valve guides (low compression).
- Other outside forces that are elevating crank case pressure. These would typically be the exhaust side of a vacuum pump in a system with a blockage.
The easiest way to check for aerodynamic forces pressurizing the case is to tie a clear plastic bag over the breather tube (preferably out of the prop wash) and have a helper observe the bag during ground run-up with the cowling removed.
- If the bag is limp, you may have aerodynamic influence in flight.
- If the bag blows up like a balloon, the case pressure is not dependent on moving through the air at high velocity.
If your bag is blown up on ground run, do a compression check, but make sure to check for leakage throughout the stroke of the cylinder all the way from top dead center to the point where the valves open. While compression may be acceptable near TDC, it may be nearly zero halfway down the stroke of the jug.
Also, pull your rocker covers and use a large screwdriver to load the valve stems while the cylinder is pressurized to check for worn valve guides and leakage. If guides are worn, loading the valve will produce leakage.
If you have turned every stone and still have excess pressure on the ground with the cowling off and good engine internals, look for things hidden in plain sight like a vacuum pump that is “supposed to have” the dump plumbed into an AOS and thus into the case.
If the main exit for the bulk of the volume of air is restricted or blocked, the only place it may have to go is into the engine, and that will cause excessive loss of oil through the AOS. (Ask me how I know …)
So … Do You Need an Air Oil Separator?
If you don’t have a wet vacuum pump (and you shouldn’t unless you have six-plus gyros or a vacuum autopilot) then you really don’t. Could you benefit from an AOS? Well if you have excessive oil loss out the breather, it would be a band-aid unless you have a very large displacement engine (radial).
The best plan is to determine where you’re losing oil.
- If it’s combustion, you have internal engine issues that will eventually need to be rectified.
- If it is out the breather, you may still have internal engine issues that need to be rectified, or more likely you are overfilling your engine with oil “because it keeps using oil, so I keep putting more in.”
Cautiously, and in a controlled manner, fly your airplane and determine if there is a point around 60 percent of filled oil capacity where your engine stops losing oil, or if instead it keeps going down regardless of level.
If it keeps going down, you have a blow-by issue. If it stabilizes, you have found the “run-at mark” for your engine (and dipstick).
Don’t assume your dipstick is correct. If your engine holds eight quarts and stabilizes at 5.5 quarts, at the next oil change add 5.5 quarts and check the stick, you may find the markings on the dipstick are incorrect. This holds especially true on twins.
My recommendation is ditch the weight, complexity, and hassles, and go without the AOS. You’ll gain some useful load, some room in the engine compartment, keep your engine healthy, and eliminate the need or desire for
the AOS.
In the modern age, I feel the AOS is an added complexity and a maintenance item that is just unnecessary.
Blue Skies, Tailwinds, & Cheap Avgas
Erich Rempert, A&P Consultant
BONUS TIP
Don’t assume your dipstick is correct. If your engine holds eight quarts and stabilizes at 5.5 quarts, at the next oil change add 5.5 quarts and check the stick, you may find the markings on the dipstick are incorrect. This holds especially true on twins.
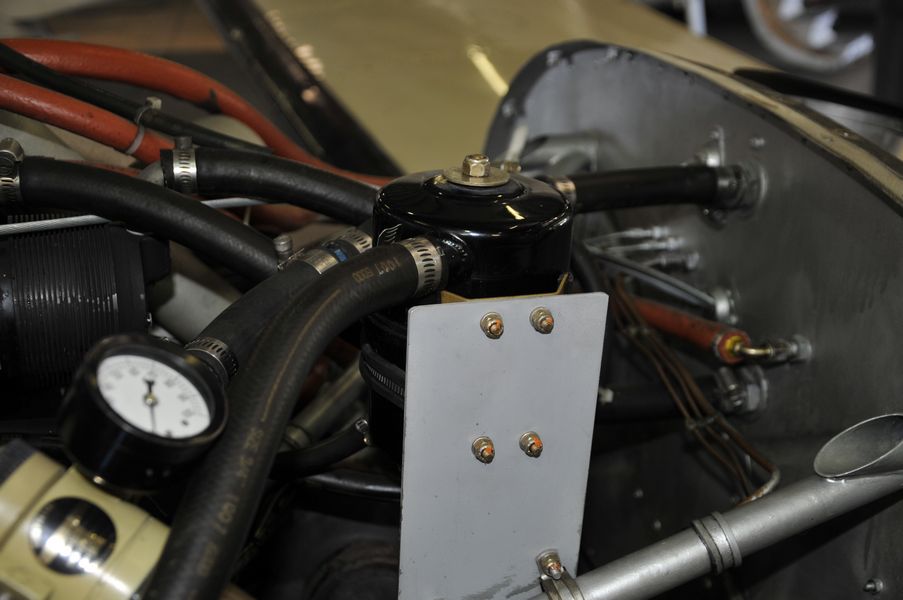
Counterpoint: Why you should get an air-oil separator. “It only takes a couple of hours to install and I recommend it highly”
By Scott Sherer
Piper Owner Society Aviation Director
There are a couple of really good reasons for owning an air-oil separator.
- I confess that I only wash my airplane once each year. And I absolutely hate washing it. It has the surface area of about four automobiles and doing the underside is a thankless job. It’s even more thankless when you get behind the engine on the lower fuselage. There’s oil and carbon mixed together and stuck on your airplane like superglue on fingertips. It’s horrible.
And while companies tout their products as simple, effortless ways to remove this horrible mess like Simple Green and Carbon X to name a couple (and they do work), why have to do it at all? Why indeed! When you install an air-oil separator, the oil stays in the engine and isn’t blown out all over the belly of your airplane. - The instructions on oil changes for my airplane say to fill my Continental TSIO-360-EB’s with eight quarts of oil. Within about five hours of flight after the oil change, my oil level was about five quarts without the separator. It doesn’t take the intellect of Albert Einstein to know that three quarts of oil has to go somewhere, right? It certainly isn’t in the engine and it hasn’t blown by my piston rings.
So where was it? It blew out of the oil breather and all over the belly of my airplane. Additionally, I had to add one quart of oil for every 8-10 hours of flight after that. And you know where that oil goes, too, right? Right! All over the belly of my airplane.
So what does an air-oil separator do? The engine has an oil breather tube that allows warm, moist, oily air from the crank case to equalize and vent overboard into the slip stream. Since your engine is hot the air in your engine is hot, too. This causes it to expand and go out the breather tube.
Your combustible gas air mixture contains large amounts of hydrogen and oxygen which combine during the combustion process creating water vapor as a byproduct. This is true in your car, too. You can see water dripping out of your exhaust pipe on a cold day.
Your engine is vibrating or bouncing and some of the oil splashes and gets mixed in with the hot, steamy air in your engine. The whole mass or should I say mess expands and blows out your oil breather. Hence, lots of hot oil mess on the bottom of your airplane.
Once you install an air oil separator, this doesn’t happen anymore. So where does the oil go now, you ask? The oil breather hose is no longer vented overboard as it was. Rather, it is routed into the separator can where the oily air is separated through a couple of internal compartments. By the time it makes it through these compartments the air is separated from the oil. The warm, moist air is once again vented overboard sans oil and the oil is drained from the separator via a different hose back into the oil pan on the bottom of your engine.
Results? The three quarts that previously blew out of the engine after an oil change are still in the engine. The one quart of oil that blew out of the engine for each 8-10 hours is still in the engine isn’t needed in the engine. When I bring my airplane in for an oil change every 50 hours or so, all of that oil is still there.
My airplane engine, which was designed in the 1960s, now has the same oil reliability as my new car does. While I still check my oil before each flight I never need to add any and it’s never low. And best of all, the belly of my airplane is, while not perfect, several orders of magnitude cleaner than it ever was.
The air oil separator that I had installed was manufactured by the Airwolf Corporation 15 years ago. It needs no maintenance and costs between $400 and $600 depending on what engine you have. It only takes a couple of hours to install and I recommend it highly.
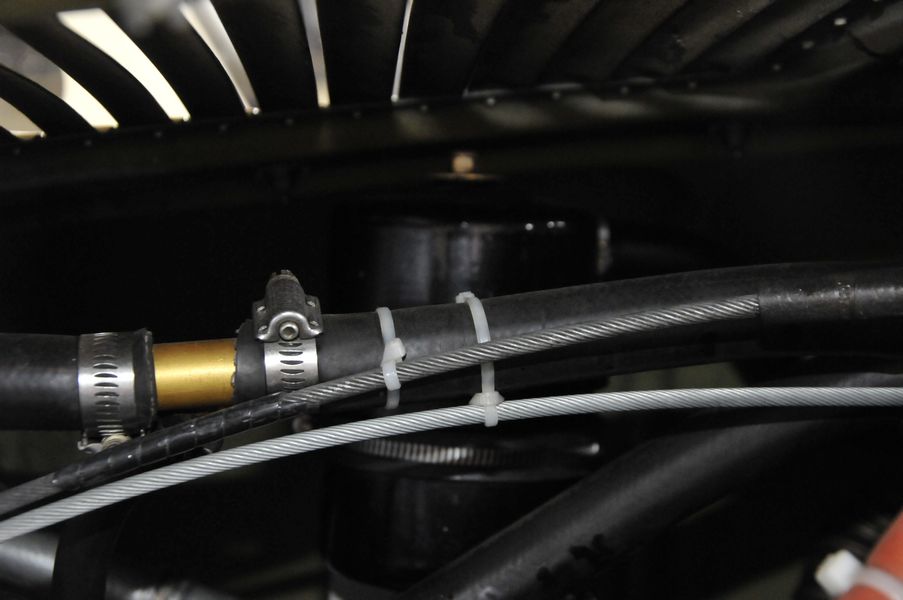
Enter the conversation: Join the discussion in the forum.