Provided by CiES
Really the story starts with “Don’t trust your fuel gauge.”
This time-honored aviation maxim was a long and distinguished cry for help. Aviation fuel level was a gauge you were supposed to have – but to cover its many vices, it was only supposed to work when it was empty.
This statement, while incorrect, allowed the mere presence of a gauge to meet the flight requirement: “Fuel gauge, yep, right there.”
The larger question of why we in the aviation community allowed a non-functional gauge to be present in the aircraft was basically ignored. The work-arounds for missing this important gauge for powered flight are numerous.
- “My fuel gauge is right here on my wrist.”
- “I have a paint stick marked with gallons of fuel.”
- “I have a fuel totalizer so that is now my fuel gauge, and it is damn accurate.”
These are all are dead wrong, but most pilots don’t know exactly why. Actually you can get into heated arguments that all of the above are truer than actually having a functional fuel gauge on your aircraft. By functional we mean a gauge that is accurate to the current fuel level onboard the aircraft to approximately 1 gallon.
How Did We Get Here?
So how did we get to these incorrect assumptions? Aircraft manufacturers of the 1950s through the 1970s utilized fuel senders designed for other applications like premium automobiles and heavy equipment to meet the fuel quantity requirements in the regulations – both CARS and FARS. Economically these were the best available at a reasonable price. In most cases the production lines that produced these senders in quantity became obsolescent for the automotive and heavy equipment industry they served, and the production tooling used in an intermittent fashion to produce fuel senders wore out or would not keep to an exact specification for the relatively small aviation market.
Importantly, these senders were not intended for aircraft, nor designed to be rebuilt or interfaced with AVGAS. Our applications in aviation were using these designs beyond their intended use – and it showed. Basically we got to “Don’t trust your fuel gauge” out of desperation of trying to push a system where it wasn’t intended to go in the first place.
Aircraft needed a specific design to address aircraft issues. Every pilot has felt the pang of not knowing exactly how much fuel they had onboard, somewhere along the way. Fuel quantity indication provided no relief, and the normal work-arounds came into play.
- Yes aircraft burn fuel at a usual rate, on most days …
- Fuel leakage doesn’t usually occur on most days …
- Mixture settings are pretty usual on most days …
- Starting fuel level is reasonably assured, on most days …
The First Solutions
The aircraft manufacturers sought to rectify the situation. Cessna moved first toward an aviation-specific design in the late ’60s and early ’70s and introduced the low-cost Pennycap system. This system was produced for an economically beneficial price structure and was not as sophisticated as those found on jet aircraft. These systems soldiered on into the ’80s. They have started to show signs of obsolescence and are not very tolerant of water in fuel and were discontinued.
Cessna, Piper, and Cirrus continued to utilize resistive senders on the bulk of their production aircraft well into the 2000s; however the FAA started to force manufacturers to limit electrical energy and wiring in all aviation fuel tanks, not just airliners. In 2008, Cessna turned to a new technology: TDR (Time Domain Reflectometry). This system bounces a signal down a coaxial cable and where the fuel touches. A signal is returned, as well as a signal from the end of the coaxial cable, providing a relative fuel level.
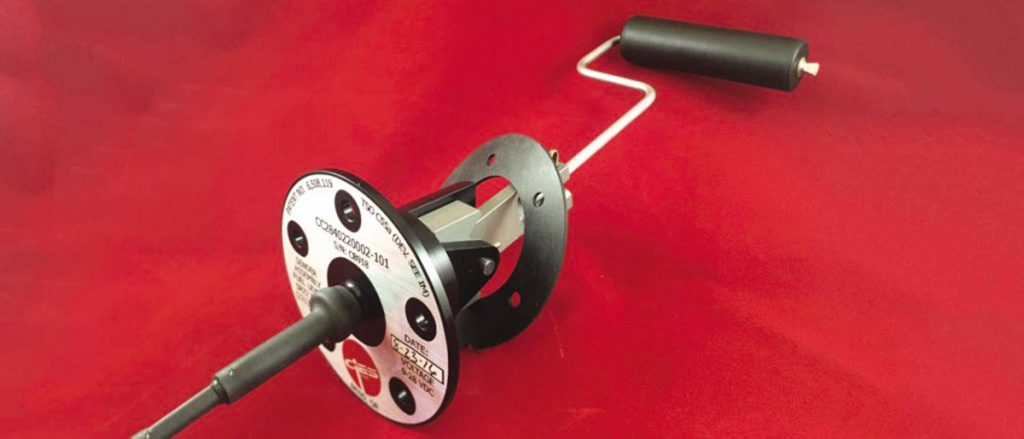
Cirrus Asks For More
Cirrus turned to CiES and we were tasked to solve the issue with the following limitations.
- It had to fit into the existing location and mounting.
- It had to interface with existing gauging as well as modern gauging.
- It had to be low cost.
If you approach the issue from the aircraft perspective, i.e. designed for aircraft, most of the traditional problems fall away. In our case we relied on the simplicity of the float, and we utilized a patented non-contact sensor to eliminate wear issues but also remove electricity from the fuel tank.
With that we paired the system to a microprocessor to address the specific output requirements for a multiple-gauge-type interface and correct for aircraft induced fuel motion.
So what have these modern systems accomplished for the GA community? Aircraft outfitted with modern fuel quantity systems like TDR and our magnetic field technology are immune from fuel-related accidents. Not just a reduction but a bull’s-eye on the issue: Zero fuel accidents.
It turns out that relying entirely on the human aspect of fuel quantity management with non- or barely functional fuel gauges was wrong and it did not produce the desired result. Pilots who relied on wristwatches, sticks, and totalizers ran out of fuel. It is evident that pilots with accurate fuel level make better fuel-related decisions, as it is very hard to argue with a complete elimination of the issue.
Now Available
Due to Cirrus’s interest in being able to retrofit a new system in legacy aircraft, the design was easily modified for most flying GA aircraft, and the FAA granted AML STC approval for over 700 aircraft types.
The CiES fuel senders utilize an active sensor which requires aircraft power to operate. This leads to running an additional wire to power the sensor, and potentially a ground wire back to some popular engine instrument systems. We typically say it will take 4-5 hours per sensor to install the system.
While we designed the CiES sender to allow it to report to legacy analog gauging (and it will), the FAA was reluctant to certify these gauges unless we had accurate gauge maps from the manufacturer. So the analog gauges we have listed are basically limited to (newer) Cessna aircraft production, as we had Cessna factory specifications for this gauge.
In the case of a new digital gauge or EIS system, CiES supports all of these interfaces as they allow calibration and gauge-mapping as part of their installation procedure.